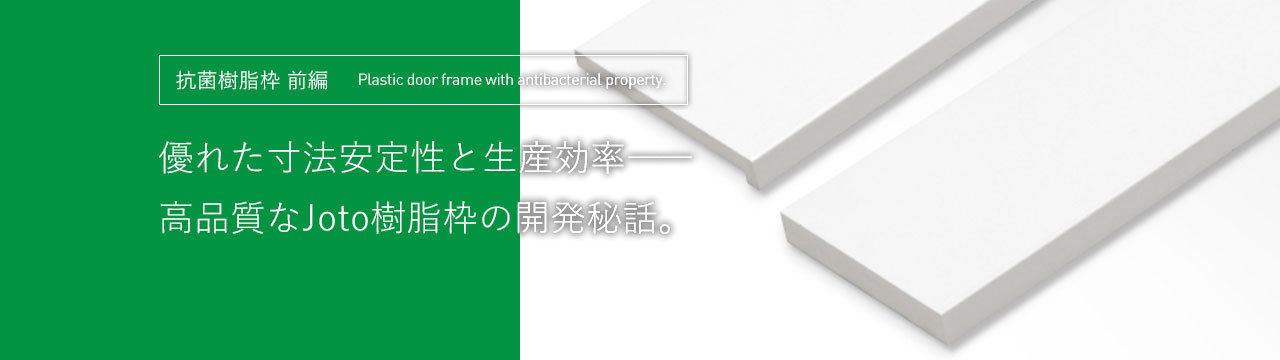
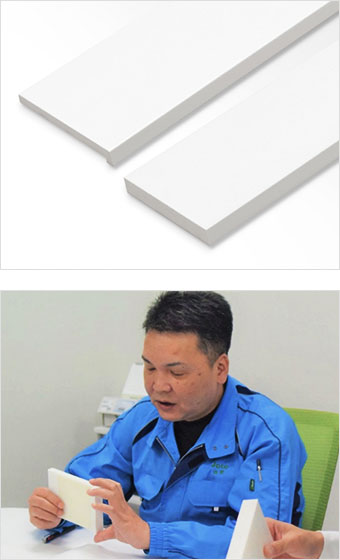
城東テクノが樹脂枠を発売したのは25年ほど前のこと。営業現場からの提案のなかに、浴室のドア枠から洗面所の床のあたりは腐りやすく、何らかの対策ができる商品を企画してはどうかとの意見がありました。当社には、当時すでに浴室周りで人気を博していた樹脂一体成形の床下点検口という商品があったので、腐れ防止として点検口とセットで提案できる樹脂製のドア枠を開発しようと考えたのがはじまりでした。
その製造方法として、日本ではあまり採用されていなかった特殊な発泡押出成形での製造を選択し、基材には塩ビを選択しました。塩ビのいいところは、自己消火性による高い安全性がある事です。また、加工時に切りカスが小口にほとんどつかない利点もありました。ポリスチレンやABSは熱で切りカスが小口にべったりとつくので、それをきれいにしないと施工ができませんが、塩ビならそのような心配はありません。原料メーカーにも協力してもらいながら原料配合を決め、製造をスタートしました。
メーカー配合された購入原料で製造をスタートしましたが、そこにはひとつ問題がありました。それは、日々の製造で何か問題があったときに原料面でのコントロールがすぐにできないことです。押出成形はその日のコンディションによって、樹脂材料の流れ方が変化します。流れが少しでも変われば、樹脂製品が凹んだり、膨れたり……。そんな時には、まずは製造装置の条件を変更して対応しますが、装置条件だけでは対応しきれない場合もあります。その場合、原料の配合を微調整することで改善できるのですが、すでに配合された購入原料では、この処置がすぐにできません。このあたりにもどかしさを感じました。
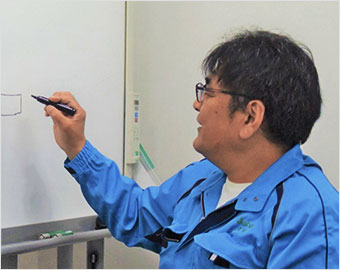
当社はもともと塩ビの押出成形が得意で、原料から社内で配合して作っていました。原料から一貫して樹脂製品を作れるのは、当社の強みです。そこで発泡押出成形の樹脂枠についても、原料から当社で製造する方針に切り替えました。原料から製造すると原料が飛散するため作業性が悪く、工場も汚れやすくなります。製造も難しくなるため、高価で高性能な製造装置が必要です。それでも優先すべきは、お客様にお届けする製品の品質と考え、原料メーカーと協力しながら検討し、色々と苦労しながら原料からの製造方法を確立させました。
また、当社は自社で金型の設計から製作まで行っています。押出成形は連続して製造を行うため、成形時の樹脂原料の流れが命です。部位によって流れが速かったり遅かったりするため、流路の設計によって成形安定性も変わってしまいます。押出機から出てくる樹脂原料をいかに上手く金型を通して、安定した製品形状に成形していくかが、金型設計の腕の見せ所です。また、当社の樹脂枠は豊富な品種を取り揃えていますが、品種が変わればノウハウが変わり、ものが大きくなればなるほど難しくなります。当社では自社製作した金型で試作を行いながら、出てくる形を見ながら金型も微調整していきます。製品の細かい寸法までこだわって作りこむことで、寸法安定性の高い製品をお客様にお届けする事ができています。
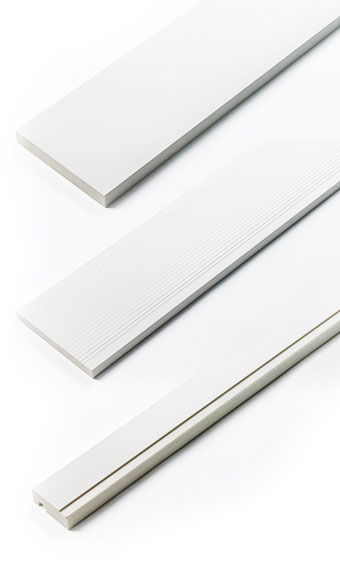
当社の樹脂枠は品種が豊富で特注対応も多く、生産時にさまざまな加工の必要が生じます。ところが、塩ビの押出成形品は熱のかかり方と冷え方にむらがあるため、見た目が真っ直ぐきれいに仕上がっていても、内部に応力が残ります。この内部応力が残った状態で切断などの加工を入れると、商品が変形してしまいます。生産後に十分な時間をおくことで、内部応力は緩和されるのですが、そこから加工を始めるのでは生産効率を低下させてしまいます。
この内部応力を解消するためには、一般的にアニールという手法が使われます。高温の炉のなかに商品を入れて、その後ゆっくり冷ますことで残留応力を解消する方法です。当社では、このアニール処理を工夫する事で効率化し、成形した商品の加工にすぐに着手することができるようにしました。このことで、製造から加工工程までの生産効率を大きく改善することができました。
当社では、原料製造から、金型の設計、押出成形、後加工工程まで、一貫して自社で取り組むことで、高い生産効率で、より高品質な製品を安定して皆様にお届けする事ができています。
- 前編
- 後編